The Jet Engine
An introduction to the invention that transformed our world.
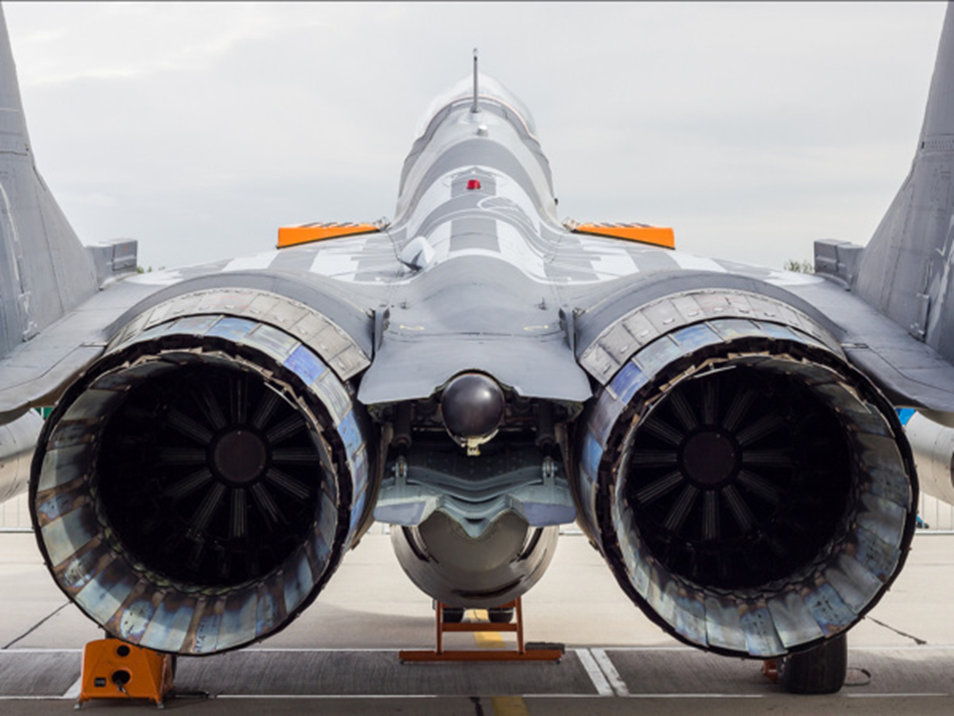
It is hard to imagine today’s world without the jet engine. It has not only revolutionised both civil and military aviation but has also left a significant mark on many other industrial fields from oil pumps to the generation of electricity. The basic premise of the jet engine is very simple: as air rushes out of the back, an opposite reactive force is in turn applied on the engine, propelling it forward. That said, due to the complexity of the engine’s multi-layered design and the variety of its permutations, an air of confusion still shrouds this vital piece of technology in the minds of many.
Brief Historical Overview
Having postulated his Third Law of Motion in 1687, Isaac Newton theorised a “steam engine” which would move by way of the propulsion from a jet of air. This kind of concept had in fact existed since antiquity; the Greco-Egyptian inventor Hero is credited with the design of the aeolipile – a simple turbine-like sphere that was spun by the passage of steam from boiling water in a cauldron below it. Over two more centuries would pass before these ideas would begin to conglomerate into something more concrete, culminating in Frank Whittle – British engineer and pilot – patenting his jet engine design in 1930. Further progress was made when German physicist Hans von Ohain, endorsed and funded by Ernst Heinkel and his company, registered a patent for his own version in 1936.
As with many nascent technologies, it was the Second World War that propelled the Jet Engine out of the laboratory and into aeroplanes. Ohain’s design was put to use in August 1939 when the experimental He 178 became the very first plane to fly solely on a turbojet engine. In July 1942, a prototype of Messerschmitt’s Me 262 fighter was also tested; unlike the British Gloster Meteor, it was the only jet that would go on to see significant active combat during the war. Although the technology came too late to have a significant impact on that war, it would take little more than a decade for a new generation of jets to sweep aside their piston piers. What exactly facilitated such a speedy and dramatic takeover?
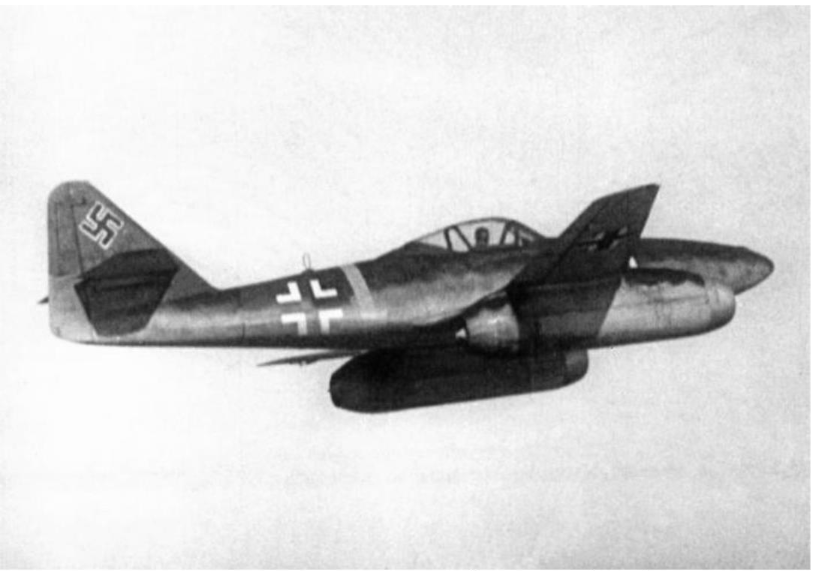
Jets vs Pistons
Although they look rather different, in many ways the two types of engines are quite similar to each other: relatives within the internal combustion family, both harness the expansion of gases following the combustion of an air-fuel mixture. Moreover, both engines typically have the same 4 general stages to their operating cycle: Intake, Compression, Combustion and Exhaust. However, in a piston engine these 4 stages/strokes occur one after the other, one at a time while in a jet engine all 4 processes are going on continuously and simultaneously in their respective parts of the engine. This crucial difference has multiple repercussions for the two engines…
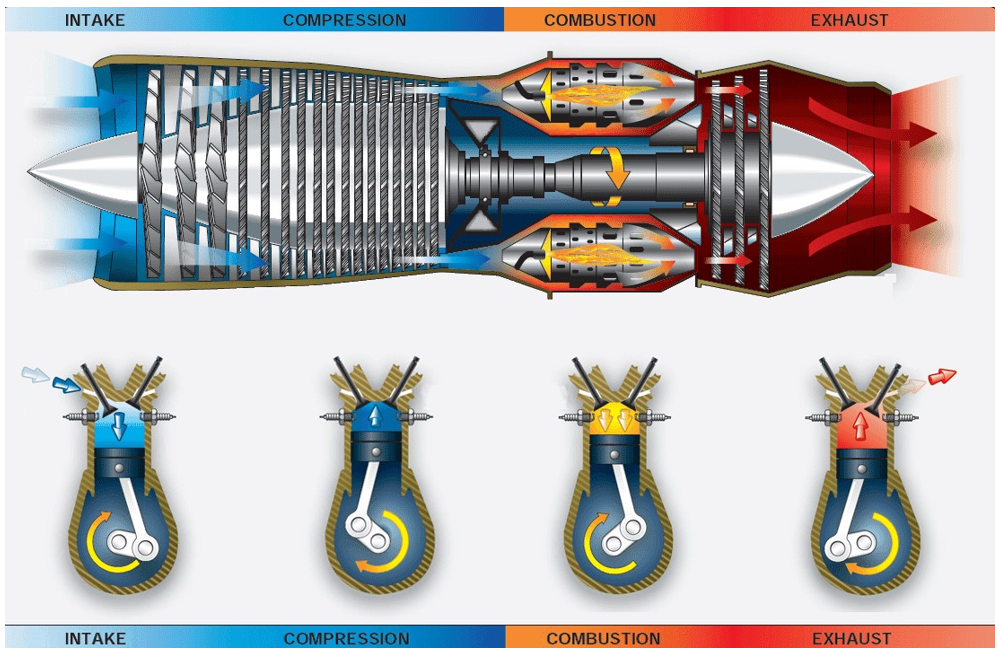
An important advantage the jet engine holds over the piston engine is its ability to reach much higher rates of RPM (Revolutions per Minute) without a detrimental drop in power output. One of the reasons most piston engines aren’t very efficient beyond around 7000 RPM is because the faster the piston moves, the smaller the time window it leaves for combustion to occur. There is no reciprocating action in a jet engine, only rotational motion, which means that there is much less risk of internal damage to engine parts caused by the force of the piston’s rapid movement at high RPM. Free from these limitations, the high-pressure rotor on a military turbofan can easily operate at 25,000 RPM.
Moreover, having fewer reciprocating parts which are constantly changing direction makes the jet engine more reliable and capable of functioning for longer periods of time before requiring maintenance to counteract any wear and tear - some commercial jet engines can run for up to 20,000 hours without a significant overhaul, 4-5 times longer than an average piston engine.
The combination of these factors meant that the jet engine’s superior reliability and thrust to weight ratio made it a much better fit for the future of large-scale aviation and all but destined to relegate the piston engine to the fringes of the civil and military spheres.
Thrust Equations
Before considering the internal structure of the jet engine, it is first necessary to understand how it produces thrust.
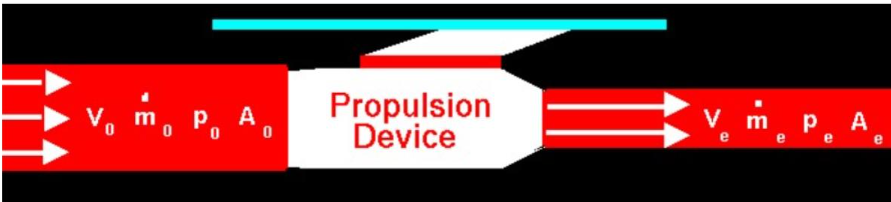
As previously mentioned, the thrust produced by a reaction engine, in accordance with Newton’s Third Law of Motion, is equal in magnitude and opposite in direction to the force exerted on the hot exhaust gases as they are expelled from its rear. From Newton’s Second Law we know that this force can be expressed as the rate of the change in the momentum of the air.
\[F = \frac{Δmv}{t}\]
\[F = \frac{m_e v_e - m_o v_o}{t}\]
Since we are dealing with a fluid, it is more helpful to consider the mass flow rate of the air - the amount of mass passing through a certain area over a period of time - rather than the mass on its own. This quantity is expressed as 𝑚̇. 𝑚̇=𝜌𝑣𝐴, where 𝜌 = density, 𝑣 = velocity of the fluid and 𝐴 = the cross-sectional area through which it is passing. Therefore, we can rewrite the equation to include the mass flow rate:
\[F = \.m_e v_e - \.m_o v_o\]
There are just two more minor factors that need to be included for a more accurate equation. The first of these is the change in mass across the engine. At first glance it seems logical to assume that 𝑚̇𝑒= 𝑚̇0, since all the air that enters the engine must subsequently come out. This isn’t entirely true, however, as there is a small mass of fuel injected into the engine. To that end we ought to add in a value "𝑓" for the fuel to air ratio; typically ranging from 1:40 to 1:130, its effect on the overall thrust output is pretty negligible.
\[F = \.m_o v_e + \.m_o v_e f - \.m_o v_o\]
\[F = \.m_o(v_e(1 + f) - v_o)\]
Another element that needs to be taken into account is the additional force that would be put on the exiting air by the difference in pressure between the air at the inlet and the outlet; this force is equal to the change in pressure multiplied by the area of the exhaust. Thankfully, the pressure at both ends of the engine is usually fairly similar and thus also has minimal effect on the total force.
\[F = \.m_o(v_e(1 + f) - v_o) + (P_e - P_o)A_e\]
Looking at this final formula and knowing that 𝑓 is negligible and 𝑃𝑒 is often similar to 𝑃0, we can deduce that the two main ways of producing more thrust are either feeding the engine a larger mass of air or accelerating that air by a greater amount.
Basic Turbojet Structure
Although the turbojet is a largely outdated design that is rarely found on modern aircraft, this basic design contains all the fundamental elements which more advanced variants will be built around. Here is a side-on view of a typical turbojet:
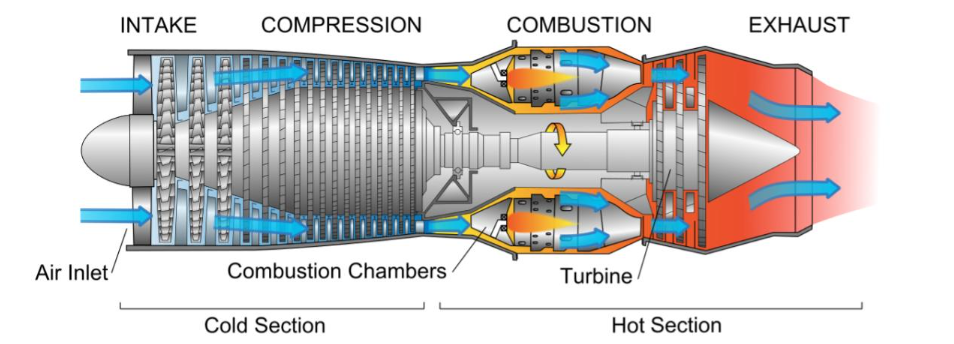
Inlet
The air’s journey through the engine starts at the inlet - the section responsible for the intake of air. Compared to the later stages, it is a fairly simple static component which is responsible for ensuring a continuous laminar flow of the freestream air ahead of it into the opening of the compressor without any turbulence.
As you would have noticed from the diagram, the air in the engine always passes through the annular spaces around the central shaft. Therefore, one straightforward way in which the airflow into the engine is kept smooth is through the addition of a nosecone in the centre of the inlet; it helps guide the incoming air away from the centre and into the openings of the inlet without the formation of any detrimental turbulence. Another important part of the engine’s inlet are the inlet guide vanes (IGV), which are located between the inner and outer cases. These thin vanes are often air-foil-shaped, similarly to the cross-section of an airplane’s wing; this makes sure that they have a minimal aerodynamic profile and do not disturb the incoming airflow.
One more aspect that needs to be considered when examining inlet function is the velocity of the incoming freestream air. For most engine designs the air entering the compressor should have an ideal velocity of about Mach 0.5 (half the speed of sound in air) with anything beyond that leading to suboptimal engine performance; this can become an issue for certain military fighters that often need to fly at speeds around Mach 2. Naturally, the inlet of their engines needs to have some way of slowing down this airflow to acceptable subsonic speeds, otherwise it would ram into the engine, leading not only to inefficiencies but also internal structural damages.
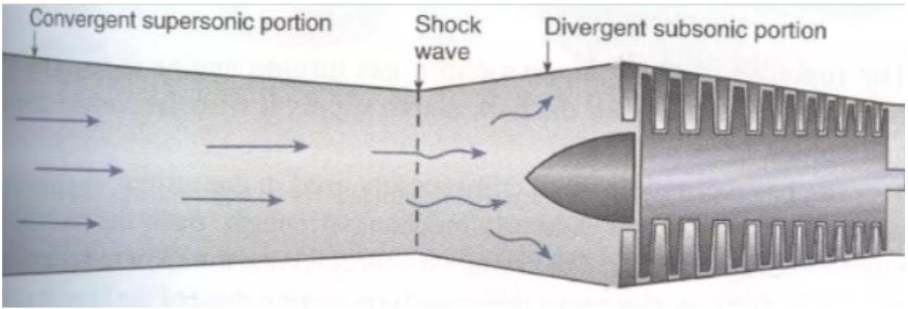
This can be solved by adding a duct to the front of the inlet; although technically considered a part of the airframe, the duct is nevertheless integral to the proper functioning of the engine. To understand why the air is slowed down in this way, we should recall the mass flow equation:
\[\.m = ρvA\]
Knowing that mass must be conserved and assuming that the air is both inviscid and incompressible (at a constant density), we can clearly see that increasing the duct’s cross-sectional area will simultaneously result in a decrease in the gas’s velocity and vice versa. This aptly explains how the incoming air is slowed down in the second, divergent portion of the duct. Indeed, the engines of a civilian jet would only require one such divergent duct immediately in front of the inlet.
At this point it also seems helpful to introduce Bernoulli’s principle, a concept we will encounter again later on:
\[P_1 + \frac{1}{2}ρ{v_1}^2 + ρgh_1 = P_1 + \frac{1}{2}ρ{v_2}^2 + ρgh_2\]
This equation stems from the principle of conservation of energy; the terms denote the Static Pressure, Dynamic Pressure, and (gravitational) Potential Energy respectively. If we were to correctly assume that the change in GPE across the duct will be negligible and also assume that the airflow is subsonic and incompressible then it becomes clear that a decrease in velocity across the duct must also be accompanied by an increase in pressure.
However, things aren’t so simple in supersonic airflow, as this type of fluid is compressible – variable in density. Bernoulli’s principle in this form no longer holds for a compressible fluid, something which is easy to deduce from our mass flow equation, as a fluctuating density would necessarily disrupt the relationship between area and velocity. For reasons beyond the scope of this dissertation, the relationship between cross-sectional area and velocity actually reverses in supersonic airflow, thus explaining the shape of the first converging portion of the duct, which serves to slow the airflow to around Mach 1. Interestingly, some complex engine designs can vary the geometry of these ducts to accommodate for airflow speed and other atmospheric conditions, with the engines of the Concorde being one such example.
Compressor
The compressor is one of the largest and most mechanically complex engine components, but why is it so important to go to such lengths to compress the air in the first place?
Ultimately, it all comes back to the thrust equation, which suggests that an increase in mass flow through the engine is one of the best ways to increase power output. Compressing the air simultaneously increases its density, which allows us to accelerate a much greater mass of air through the engine per unit of volume and also helps facilitates a more efficient rate of combustion in the burner.
Axial vs Centrifugal
There are two main types of compressors: axial and centrifugal compressors, with the key conceptual difference between the two being the direction of airflow: in an axial compressor the air travels parallel to the compressor’s shaft while in a centrifugal compressor (sometimes also called a radial compressor) the air travels perpendicularly to the shaft as it is flung out towards the edge. Although some early turbojet designs utilised centrifugal compressors, most modern engines prefer the axial variant.
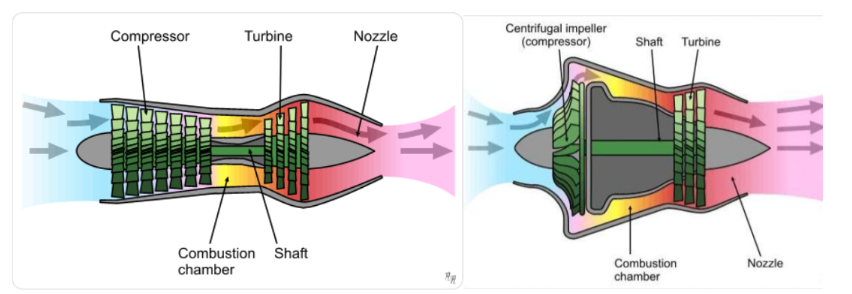
The centrifugal compressor has numerous disadvantages which make it inferior to its counterpart in many scenarios. As has often been reiterated, drawing in larger quantities of air is key to optimal engine performance. Visualising both compressors from the front, we can clearly see that the cross-sectional area through which the centrifugal compressor takes in its air is a relatively small portion of its total front-facing area; in the axial compressor, meanwhile, practically the entire inlet area is used. This effectively means that a centrifugal compressor would need to be almost twice as wide in diameter to take in the same volume of air as an equivalent axial compressor, which brings serious negative ramifications regarding aerodynamics and weight – quantities which are always of paramount importance in aircraft design.
Moreover, another advantage of the axial design is the ease with which successive stages can be stacked one after the other; modern military engines can demand compression of up to 20 atmospheres before combustion - practically impossible to achieve without the multitude of compressor stages that an axial compressor can provide. It is intuitively obvious from the diagrams above that a compressor consisting of multiple centrifugal stages would be rather inefficient because the general airflow would be forced through a number of harsh right-angled turns as it is sequentially directed out to the edge and then back into the centre of the impeller, which would inevitably result in a noticeable loss of energy. This angularity of airflow – standing in stark contrast to the air’s straight path through the axial compressor - is in fact a general problem with the centrifugal design that is only magnified when multiple stages are added.
Structure
With the axial compressor being the more common type of compressor, it would be prudent to take a closer look at its inner workings and structure. Each of the axial stages consists of two main components: a rotor and a stator, displayed below on a macroscopic and a more local level. The rotors in the compressor are connected to each other and rotate uniformly at the same RPM, with several bearings being added to the assembly to ensure that the structure is balanced and able to rotate smoothly.
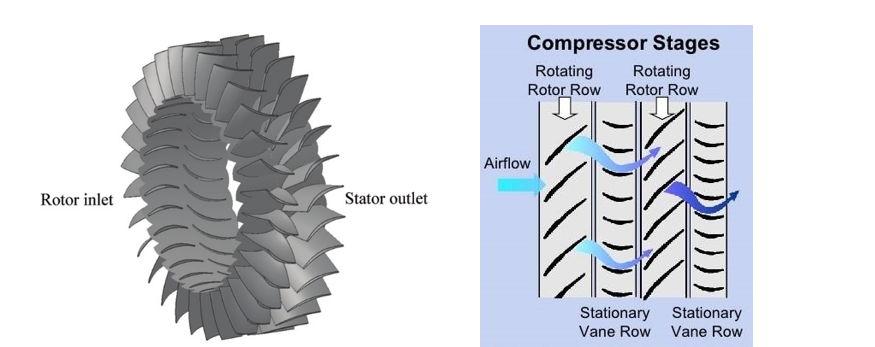
As expected, just like the inlet guide vanes, the blades of both the rotor and the stator are usually airfoil shaped to best facilitate the turbulence-free passage of air through the compressor. When the rotor spins, these fast-moving blades push the air forward, doing work on it and thus increasing its velocity and kinetic energy. The stator blades (often called vanes) then slow down the incoming air; this decrease in kinetic energy, in correspondence with Bernoulli’s aforementioned principle, is simultaneously accompanied by an increase in the air’s pressure as it is forced into a progressively smaller space. Something else worth mentioning is the fact that the stator vanes are angled oppositely to the rotor blades, which helps “straighten out” the airflow, guiding it along a more-or-less straight course through the compressor and stopping it from needlessly swirling around.
Compressor Stall
One of the greatest hazards facing jet engines is that of compressor stall, which occurs when the airflow through the compressor becomes turbulent or begins to change direction and move backwards, pushed out by the higher pressure within. This can happen to the air passing over a single airfoil shaped blade, an entire compressor stage, or indeed several stages simultaneously, in which case a phenomenon called engine surge may occur: with the airflow to the combustion chambers having been momentarily disrupted, the air-fuel mixture within is disturbed and combustion becomes irregular. This is usually accompanied by a sudden spike in internal engine temperature, violent vibrations, and loud bangs; in some cases, the engine can even be momentarily seen spouting out flames and total engine failure is a legitimate risk.
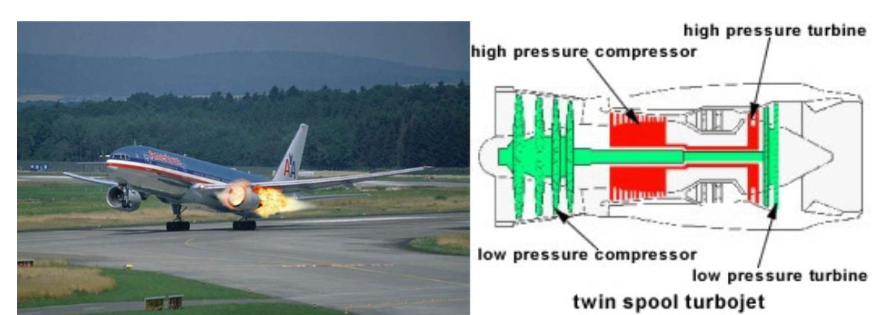
One large-scale modification to engine design that not only helps ameliorate the pressing issue of compressor stall but also generally improves engine efficiency is the dual-rotor/twin-spool engine. In fact, the vast majority of modern jet engines utilise this variant over the more simplistic single-rotor variant. The dual-rotor helps mitigate inefficiencies by allowing each of the two compressors to rotate at its own optimal RPM.
Other notable ways of reducing the risk of compressor stall include the addition of air bleed ports along the compressor case which are automatically opened and closed during flight periods when stall is likely, serving to relieve the build-up of pressure that can lead to the reversal of airflow. Some engines also employ variable angle stator vanes on the first few stages; the position of these blades can be fine-tuned by a hydraulic system to present the most optimal angle of attack.
Combustor
Before moving into the combustion chambers, we must first pass through the intermediate diffuser section. This is simply a divergent case which, in accordance with Bernoulli’s principle, simultaneously slows down the airflow and increases its static pressure, thus helping further set up the ideal conditions for combustion in the burner.
The combustion section (informally referred to as the “burner”) can really be considered the heart of the jet engine, as this is the key place where the acceleration is provided to the air and where the core energy transfer within the engine takes place. Needless to say, the combustion reaction that happens here is a highly exothermic one in which the chemical energy stored within the jet fuel is transferred to the kinetic and thermal stores of the airflow.
Jet fuel is sprayed into the chamber through nozzles in a fan-like pattern for thorough mixing with the oxygen in the air. Once ignited by a starter plug, unlike in a four-cycle piston engine, combustion continues uninterrupted until the engine is switched off. Given that the flame shown on the diagram usually reaches a temperature in the region of 2000 degrees Celsius, it is imperative that it doesn’t come into direct contact with the combustor’s walls, as even the most heat-resistant metals would be at risk of melting.
This is prevented by diverting over 75% of the incoming airflow around the central entrance to the burner and directing it along its walls, where it then enters through a plethora of holes; this provides a “blanket” of cooler air around the inside of the walls and keeps the hot air and flame restricted to the middle of the can. The hot and cool air mix at the exit and their temperature becomes largely homogenised.
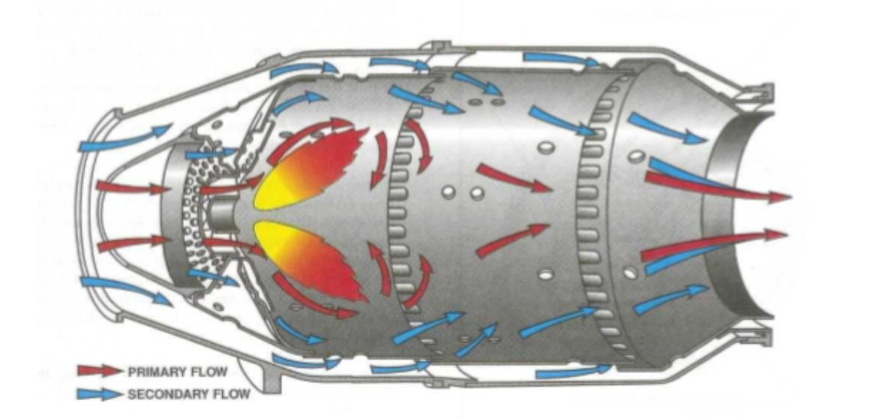
There are two main types of combustor design: the multiple can (tubular) set up and the annular combustor. Most of the differences between the two are spelled out by their names; the tubular combustor separates the airflow from the diffusor into several burner cans, in which combustion occurs and is contained. This is the older of the two variants and, although once omnipresent, is rarely found in today’s high-performance turbojets and turbofans. That said, this set up, although more complex structurally, is easier to service and maintain, as each individual “burner can” can be removed and inspected separately for damages without a total disassembly of the entire engine.
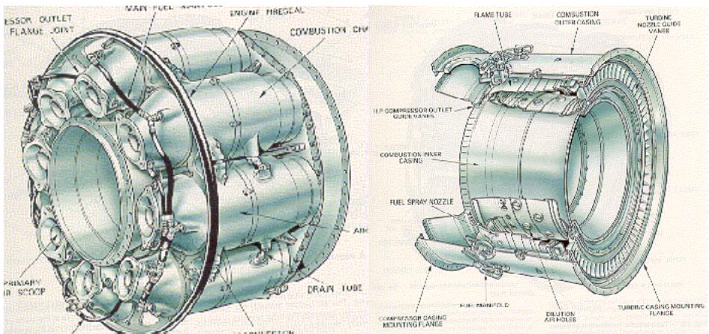
Meanwhile, all the combustion in an annular combustor takes place in the ring-shaped space between the inner and outer case. There are numerous advantages to this design; it is more compact, lighter, and doesn’t require the complex system of ducts needed to smoothly separate the air at the inlet of the tubular set up and then recombine it at the outlet. Moreover, combustion in the annular design is generally more uniform – as would be expected from a single chamber – resulting in more even temperatures at its exit, which is beneficial for turbine function. A compromise between the two comprised of a ring of burner cans stationed within an annular case also exists; this can-annular variant is less common than the annular design but usually preferred over the tubular one.
Turbine
Knowing that the compressor’s rotor blades do work on the air as they collide with its particles, the question of where this energy comes from naturally arises. In fact, it is the rotation of the turbine – connected directly to the compressor’s rotor through the central shaft – that drives the compressor. Therefore, the turbine needs to be designed to extract enough energy from the hot gases exiting the combustion section to meet the compressor’s demands.
Although the turbine may look quite similar to the compressor in shape, because of the very different role it performs within the engine it has a number of important structural differences. Just like the compressor, the turbine also consists of alternating rotating and stationary disks, with a crucial difference being the inversion of the order: in each turbine stage the stationary components (collectively referred to as a turbine nozzle rather than a stator) are placed in front of the rotor. This is done to ensure that the nozzle guide vanes can direct the gas flow into the rotor blades at the most forceful angle, so as to be able to efficiently extract enough kinetic energy from the air to turn the compressor’s rotor. Moreover, the nozzle guide vanes also help increase the velocity of the air before it collides with the rotor blades by passing it through what is effectively a convergent duct.
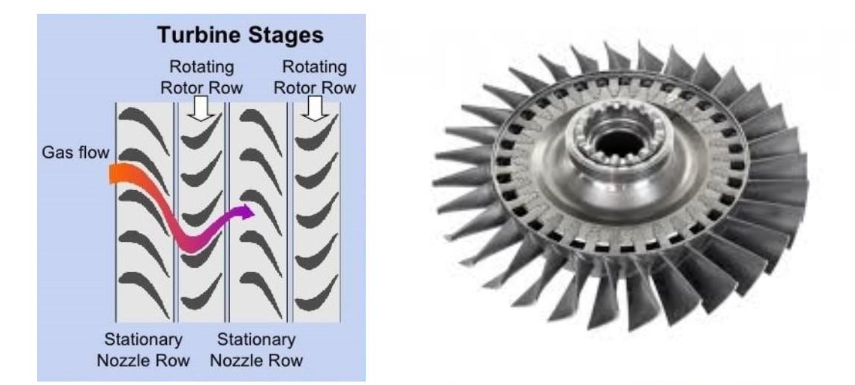
As opposed to the typical axial compressor, which carries out its job through a multitude of small bite-sized chunks, the turbine’s structure allows for the extraction of a great deal of energy in one go; it thus only needs to be composed of three or four stages. Furthermore, whereas each successive compressor stage is smaller in diameter, the turbine stages instead become increasingly larger to compensate for the fact that there is progressively less energy available for extraction.
Nozzle
The exhaust gases lose about 60% of their initial energy by the time they exit the turbine section and enter the exhaust duct (nozzle) – the last step before leaving the engine for good. Similar in many ways to the inlet, the nozzle is also a simple engine component which nevertheless has a significant impact on engine performance and thrust output. One structural similarity between the two that is immediately noticeable is the tail cone, which – just like the nose cone – helps to keep the gas flow streamlined and laminar.
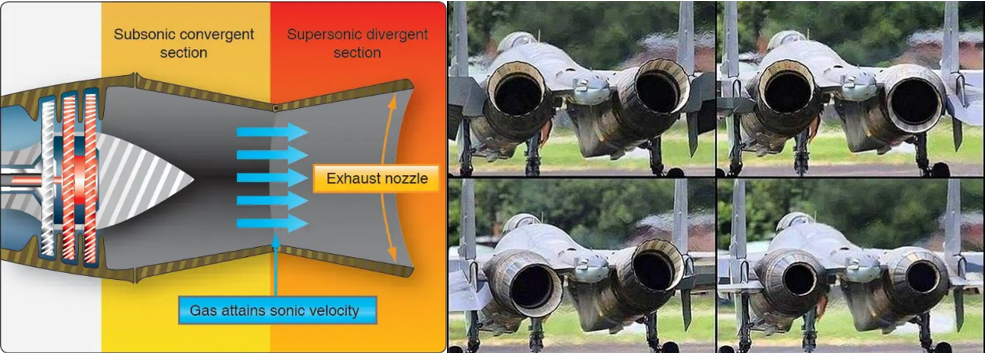
The primary function of the nozzle is to maximally accelerate the exhaust gases before seamlessly releasing them back into the free airstream. By now we know that the best way of manipulating fluid velocity and pressure is through the choice of duct shape. Most subsonic and transonic planes’ engines settle for a convergent nozzle which will accelerate the exhaust gases to near-supersonic speeds prior to existing. Supersonic military jets on the other hand (coincidentally also thSe planes likely to have a convergent-divergent inlet duct and an afterburner) will typically require a convergent-divergent exhaust duct to speed up the air to Mach 2 and beyond.
These high-performance engines often also employ a variable area exhaust nozzle which can change the shape of its opening in accordance with the amount of thrust demanded by the pilot. The complexity of nozzle designs has in fact gone even further in recent decades, with most new generation fighter planes having thrust vectoring capabilities; a technology first introduced by the vertical take-off of the British Harrier, it provides the nozzle with the fascinating ability of changing the direction of thrust during high-intensity manoeuvres by angling itself in the necessary manner.
Metallurgy and Superalloys
Undoubtedly one of the most complex and challenging parts of this field worthy of its own separate inquiry is that of selecting the correct materials for the interior of the jet engine. As we all know by now, the components of the engine must not only maintain their structural integrity through blisteringly high temperatures and pressures but also be able to withstand the strains of incredible centrifugal forces and resist “creep” - the tendency of metals to gradually deform over time when subjected to persistent mechanical stress.
A discussion about metallurgy should certainly focus on the high-pressure turbine: receiving the full brunt of the exhaust gases from the combustion chambers and often having to endure temperatures as high as 1500 degrees, it is the single engine component exposed to the harshest environment. Therefore, in addition to being internally air-cooled by a specially-designed system which re-routes a portion of airflow from the compressor to the turbine, it is imperative for the turbine blades to be composed of an incredibly robust and heat-resistant material – a superalloy. Of the three possible elements which superalloys can be based on, Nickel is generally the preferred option over Iron and Cobalt because it is a little cheaper than the latter and maintains the same FCC (Face Centred Cubic) structure right up to its melting point.
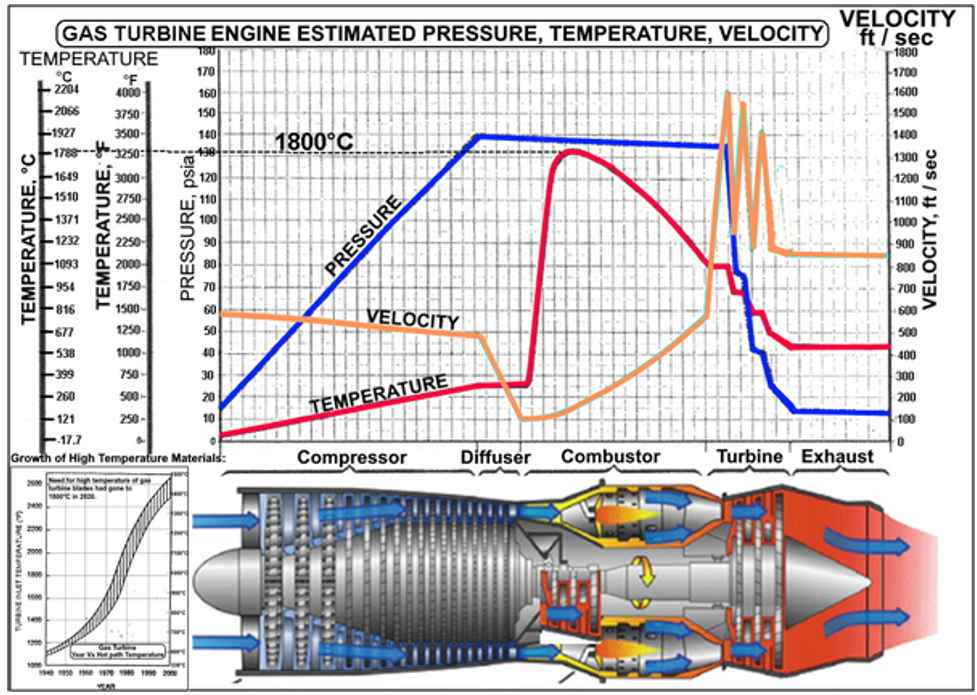
Despite most metals and metal alloys having a relatively high melting point, we see a drastic drop in their strength characteristics at temperatures well below it due to the increased energy of the atoms making it easier for the processes of diffusion (the gradual movement of atoms through the metal lattice) and dislocation (the movement of irregularities within the crystalline structure) to occur when stress is applied. It is primarily their structure - a clever combination of the γ and γ' phases -that helps these superalloys restrain diffusion and dislocation and thus better maintain their strength at high temperatures.
The γ phase (shown on the left of the diagram) is effectively the default state that Nickel-based alloys take when only a small amount of Aluminium is added; the distribution of the two elements is largely random and it is relatively easy for diffusion and dislocation to occur, as any vacancy in the lattice can be filled by either type of atom. In contrast, there is enough Aluminium in the intermetallic γ' phase to form its own lattice within the alloy; it is much harder for diffusion to take place when a vacancy appears in this lattice because all the nearest atoms are Nickel atoms, for which the energy barrier to fit into the Aluminium lattice is much higher.
As a result, rather than acting like a metal, the intermetallic γ' phase displays the same hard and brittle qualities that one might expect from a ceramic or glass-like substance; the turbine blades would be far too fragile and fracture-prone if they were exclusively composed of this phase. The carefully-balanced compromise that scientists have come up with consists of nanoscopic “bricks” of γ' sitting within a “cement” of γ; in this arrangement the continuous γ phase allows the turbine blade to maintain enough ductility while the γ' sections - making up 65%-70% of the entire structure - provide the necessary strength and heat resistance.
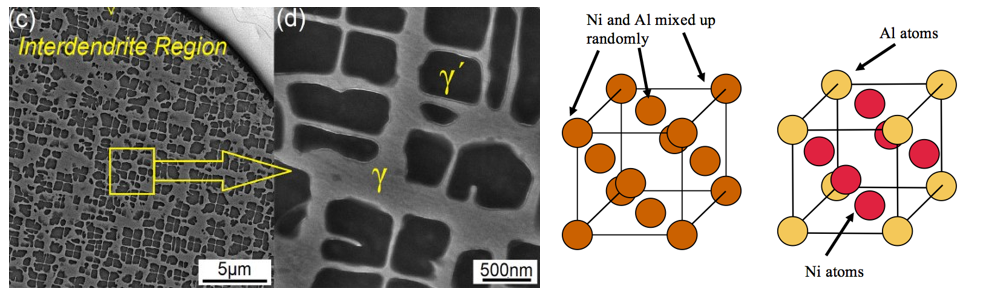
Another way that we can help restrain diffusion and dislocation in the superalloy is by forming the whole blade as one single crystal by passing it through a spiral-shaped grain selector when solidifying. The typical polycrystalline structure found in metals becomes a liability at high temperatures because the grain boundaries can act as high-speed pathways for diffusion and could also weaken the structure by allowing the individual grains to slide along each other. Many other metals are added to further strengthen and optimise the superalloy: Chromium for better resistance to oxidation; Molybdenum, Iron, and Cobalt to strengthen γ phase and Tungsten, Titanium, Niobium, and Tantalum to strengthen the γ' phase. The blades are also coated in a protective ceramic layer of Zirconia for even better resistance to heat and oxidation.
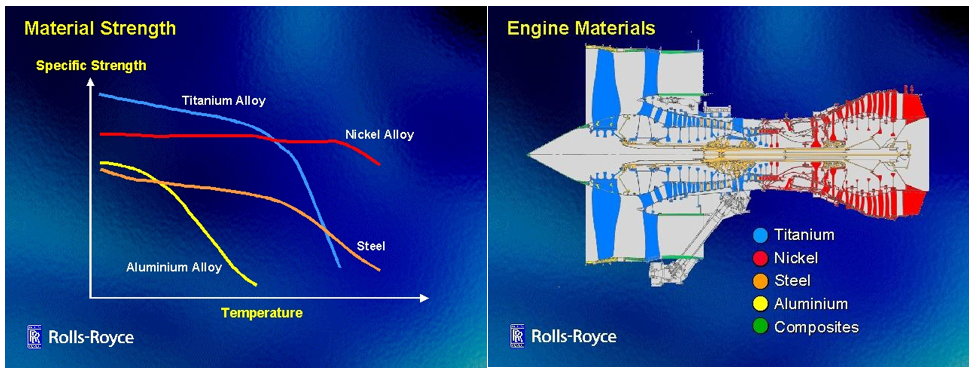
Similar Nickel-based alloys are also typically used for the casing of the combustion chambers – another engine section which is regularly subjected to temperatures of around 1000 degrees - and the last couple of stages on the high-pressure compressor. In earlier parts of the compressor the temperature is low enough for the blades to be made from Titanium-based alloys which are weaker but also lighter than the superalloys, a factor which is always in consideration with anything airplane-related.
Variations on a Theme
Having examined the structure of a simple turbojet engine, we have familiarised ourselves with the basic gas generator set up (compressor + combustor + turbine sections) which will come to form the foundation of these more complex variants of the gas turbine engine.
Afterburners
Given that only a small portion of the total air passing through the gas generator is combusted in the burner section, there is still a great amount of untapped energy available for exploitation left over in the exhaust gases leaving the turbine. The afterburner/augmenter is an important additional engine component predominantly found on modern fighter and interceptor aircraft which can be used to produce immense increases in thrust by accelerating the air even further prior to releasing it from the engine. Thrust output can readily be augmented by some 50% by the afterburner, albeit only for short periods of time – such as taking off or chasing down an enemy plane – since utilising the afterburner doubles or triples the airplane’s fuel consumption during those moments.
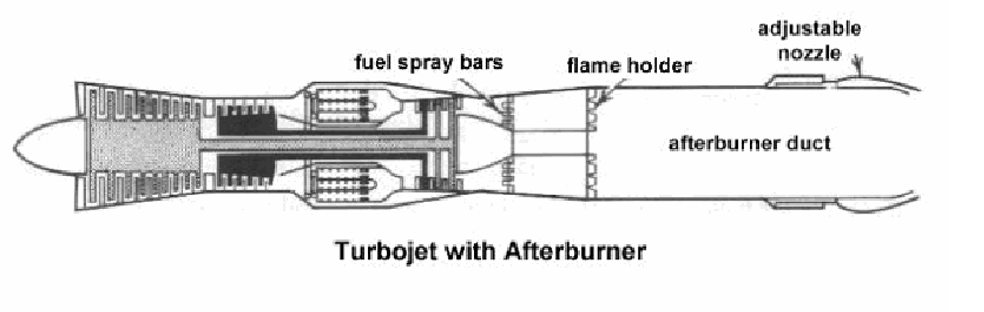
Although usually the single largest engine component, the afterburner is simply a long duct between the turbine and exhaust nozzle in which additional combustion can occur. The entrance to the afterburner duct takes a divergent shape for the same reasons as the diffuser: to slow down the airflow for more efficient and steady combustion later on. A flameholder is also installed for this purpose; visually contrasting with the elegant, streamlined engine components we have become so accustomed to seeing, the flameholder’s jagged and angular design disrupts and slows down the airflow, thus facilitating thorough mixing with the jet fuel before combustion occurs.
Similarly to the combustor, some of the exhaust gases flow through the annular space of a special liner before passing back into the afterburner through holes in the duct’s walls. This not only serves the vital purpose of confining the hot flame to the centre of the duct but also brings the extra benefit of reducing the unpleasant “screeching” noise produced during afterburner operations.
Turbofan
Of all the jet engine variants, the turbofan is the design that continues to be the most dominant in the spheres of both civil and military aviation. It isn’t difficult to deduce that the main difference between the turbofan and the turbojet is the addition of a “fan” to the front of the engine. This fan serves a dual purpose: the inside of the fan effectively acts as the first one/two stages of the compressor, drawing air into the core of the engine; meanwhile, the outside of the rotating fan plays a role not too dissimilar from that of a propeller, doing work on the air which will not enter the engine core/gas generator and accelerating it as it passes through its blades.
This is the key to the turbofan’s superiority over its predecessor, as this design can produce greater amounts of thrust from the same amount of fuel burned by accelerating a larger mass of air with its fan. Naturally, as it now also has to bear the additional burden of turning the fan, the turbine needs to be larger and have more stages than that of the turbojet. In addition to being more fuel efficient, turbofans also tend to be noticeably quieter than turbojets – yet another reason they are the preferred engine for passenger airliners.
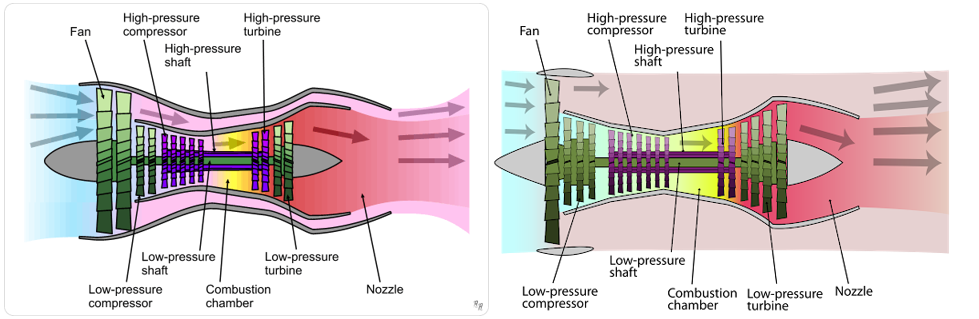
Not all turbofans are the same, however, with one structural difference immediately visible from the two diagrams above being the presence or absence of a duct to recombine the fan and core exhausts at the back of the engine. Arguably a more significant source of variation is the concept of the bypass ratio - the quantitative relationship between the mass of air which flows around the engine core and that which is actually taken into the gas generator. A turbofan found on a typical passenger aircraft such as the GEnx could have a bypass ratio as high as 9:1, thus most of such an engine’s thrust tends to come from the work done on the air by its massive fan, rather than the velocity of the gases leaving the nozzle.
On the opposite end of the scale we have today’s military engine of choice – the augmented turbofan (a ducted turbofan with an afterburner) – some versions of which have bypass ratios well below 1:1. It is logical that aircraft designed for high-speed missions would prefer a more streamlined engine which focuses on maximally accelerating the air, rather than simply drawing in a large mass.
Turboprop
Conceptually, the turboprop design can be seen as the high-bypass turbofan taken to the extreme; instead of an enclosed fan, an entire propeller is attached to the front of the gas turbine. As with the fan, the rotation of this massive propeller is driven by the low-pressure turbine. However, rather than being directly attached to the rotating shaft of the low-pressure turbine and compressor, this is done indirectly through a reduction gearbox. A gear reduction of 10:1 would usually be necessary – bringing the compressor’s 15,000/20,000 RPM to a more manageable 1,500/2,000; due to the propeller’s much greater diameter, spinning at so great RPM would cause the tips of its blades to break the sound barrier, putting excessive strain on them through centrifugal forces and creating inefficiencies in the handling of airflow.
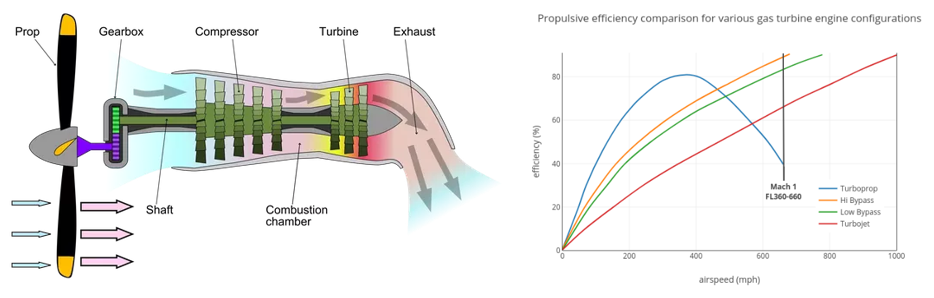
Almost the polar opposite of the turbojet, turboprops produce the vast majority of their thrust from the large quantities of air moved by the propeller. As a result of heavily prioritising mass flow over acceleration imparted, turboprops perform very efficiently at low airspeeds and have excellent take off and acceleration characteristics; these qualities make it the perfect fit for airlines operating smaller planes which need to make frequent trips over relatively short distances. Unfortunately, due to the inherent flaws of the propeller in a compressible medium with shockwaves, the turboprop operates poorly at transonic and supersonic speeds beyond about 700 km/h.
Turboshaft
While all the variants we have seen up to this point have been focused around the aviation industry, the turboshaft is truly unique in the way it displays the true versatility of the gas turbine setup. The distinguishing feature of the turboshaft is the addition of a free turbine to the back of the gas generator which can rotate independently and is connected to an output power shaft. Ideally, this free turbine should extract almost all the energy from the airflow passing through it, at which point the exhaust gases can be suitably released; since the turboshaft’s power comes from the shaft’s rotation, rather than the velocity of these gases, it is not rated in newtons of thrust but in shaft horsepower - up to 50,000 horsepower on the greatest engines.
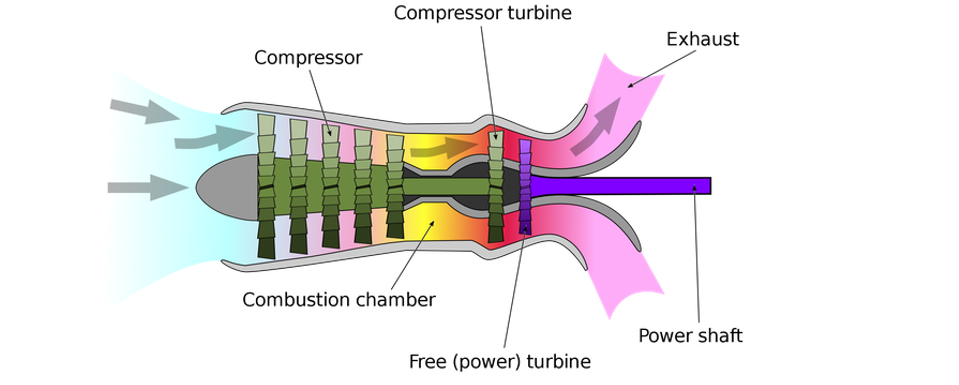
A multitude of industrial uses have been found for this power, from turning crude oil and natural gas pumps to driving electrical generators. The turboshaft has also filled an important niche among its relatives in the sphere of aviation: its light weight and high power output make it a great fit for helicopters, yet it can also be used on airplanes as a form of turboprop if the design is modified to direct the output shaft through the gas generator and out the front. As surprising as it may sound, the turboshaft has in fact spearheaded the spread of the jet engine beyond the air force and into other military branches; today it is not only often used to power the propellers of ships but has even replaced the reciprocating diesel engine in some modern tanks like the American M1 Abrams.
Ramjet and Scramjet
Moving beyond the effective speed of the turbojet and turbofan, we find the ramjet and scramjet. Although the basic concept of the ramjet was patented as early as 1913 by French inventor René Lorin, it would take half a century before this design – simple in theory but complex in execution – would truly begin to secure its place in the sectors of aviation and missile technology. While it does perform the four basic stages of intake, compression, combustion, and exhaust like the other jet engine variants, the crucial structural difference that separates the ramjet from these other designs is the absence of the gas generator core that we have become so accustomed to seeing.
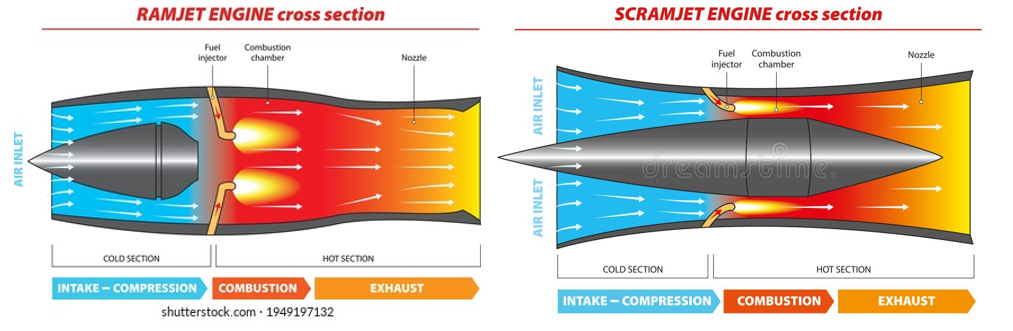
The question of how the ramjet can adequately compress the air for combustion without the complicated compressor assembly naturally arises. As it turns out, at speeds of Mach 2.5/3 and beyond, the “ram-effect” from the formation of shockwaves around the inlet and the passage of the airflow through a convergent-divergent duct is enough to sufficiently increase its pressure while also slowing it down to subsonic speeds for combustion. Since there is no compressor, the need for a turbine to drive it also disappears, which means that the ramjet can have a much simpler design with fewer complex moving parts, making it well suited for efficient operations in the Mach 3 – Mach 6 range.
Beyond this speed the increase in temperature and pressure from the ram-effect is too great for the ramjet to function safely and efficiently - this is where the scramjet (supersonic combustion ramjet) comes into play. A relatively new design, it takes advantage of the fact that, at hypersonic speeds, even slowing the air down a bit is enough to raise its pressure to combustion levels; therefore, the airflow through a scramjet can remain supersonic, even in the combustion section.
Unfortunately, the ramjet and scramjet both have a substantial drawback: only being able to effectively compress air when travelling very quickly, these engines can’t function at subsonic speeds and have no way of producing static thrust for take-off. As a result, it always has to be combined with another form of propulsion to provide the vehicle’s initial acceleration - usually another jet engine in the case of an airplane and a rocket in the case of a missile. The futuristic-looking SR-71 actually used two complicated “turboramjet” engines; the design effectively acted as a turbojet with an afterburner until the necessary speed was reached, at which point the air would be made to bypass the turbojet and flow straight to the afterburner, very much like a ramjet.
With some scramjet-powered hypersonic missiles already capable of reaching speeds up to and above Mach 10, it remains unclear just how far the scramjet can take us into the hypersonic range.
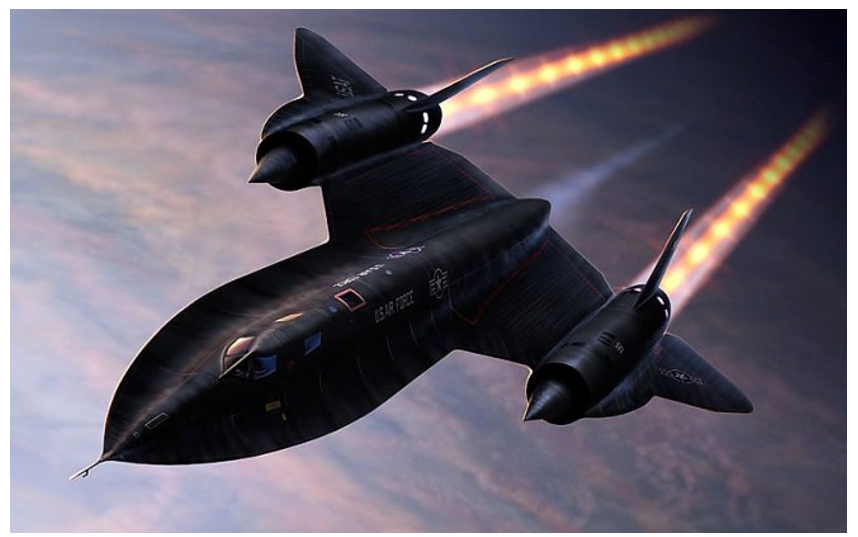
Conclusion
We have not only got to grips with the inner workings of this marvellous machine but also seen the full range of applications for its many variants. Will the aviation industry continue to perfect the high-bypass turbofan, making it ever more fuel-efficient and adapting it to more eco-friendly fuels? Will development of ramjet and scramjet technology make subsonic flight a thing of the past? One thing we can say for certain is that the jet engine has proven itself to be worthy of its place among the list of inventions most responsible for the technological progress of mankind.
Bibliography
Badeshia, H. K. D. H. (2003). Nickel Based Superalloys. Retrieved from: http://www.phase-trans.msm.cam.ac.uk/2003/Superalloys/superalloys.html
Baxter, Alexander, and Ehrich, Frederic. (1999). Jet engine, type of internal combustion engine. Retrieved from: https://www.britannica.com/technology/jet-engine
Benson, Tom. (n.d.). General Thrust Equation. Retrieved from: https://www.grc.nasa.gov/www/k-12/VirtualAero/BottleRocket/airplane/Animation/turbtyp/ettm.html
Cervenka, Michael. (2000). The Rolls-Royce Trent Engine. Retrieved from: https://www.phase-trans.msm.cam.ac.uk/mphil/Trent1/sld001.htm
Duggappa, Divya Vadegadde. (2015). Alloys and aircraft. Retrieved from: https://www.stem.org.uk/system/files/elibrary-resources/2016/01/Catalyst_26_2_633.pdf
Gavrieli, Kfir, Nora, Salim and Yañez, Armando. (2004). The Jet Engine: A Historical Introduction. Retrieved from: https://cs.stanford.edu/people/eroberts/courses/ww2/projects/jet-airplanes/index.html
Hall, Nancy. (last updated 2021). Bernoulli’s Equation. Retrieved from: https://www.grc.nasa.gov/www/k-12/airplane/bern.html
Hall, Nancy. (last updated 2021). Ramjet Propulsion. Retrieved from: https://www.grc.nasa.gov/www/k-12/airplane/ramjet.html
Ijaz, Faisal. (2023). Nickel Super alloys – the need of the modern aerospace industry. Retrieved from: https://medium.com/@faisal_ijaz1991/nickel-super-alloys-the-need-of-the-modern-aerospace-industry-7ffd7fbb1552
Okura, Takehiro. (2015). Materials for Aircraft Engines. Retrieved from: https://www.colorado.edu/faculty/kantha/sites/default/files/attached-files/73549-116619_-_takehiro_okura_-_dec_17_2015_1027_am_-_asen_5063_2015_final_report_okura.pdf
Pilot Institute (2023). Turbofan vs. Turbojet: What’s the Difference? Retrieved from: https://pilotinstitute.com/turbofan-vs-turbojet/
Shaw, Robert J. (last updated 2023). How does a jet engine work? Retrieved from: https://www.grc.nasa.gov/www/k-12/UEET/StudentSite/engines.html
Wenzel America (2021). Turbine Blades and Superalloys. Retrieved from: https://www.wenzelamerica.com/turbine-blades-and-superalloys/