Talking Engineering: Andy Reynolds
It is estimated that the Aviation sector accounts for 3.5% of global warming, releasing into the atmosphere more than 900 million tonnes of CO2 per year. Airbus, the world’s largest aircraft manufacturer, is at the forefront of research into sustainable aviation, and is pioneering the development of
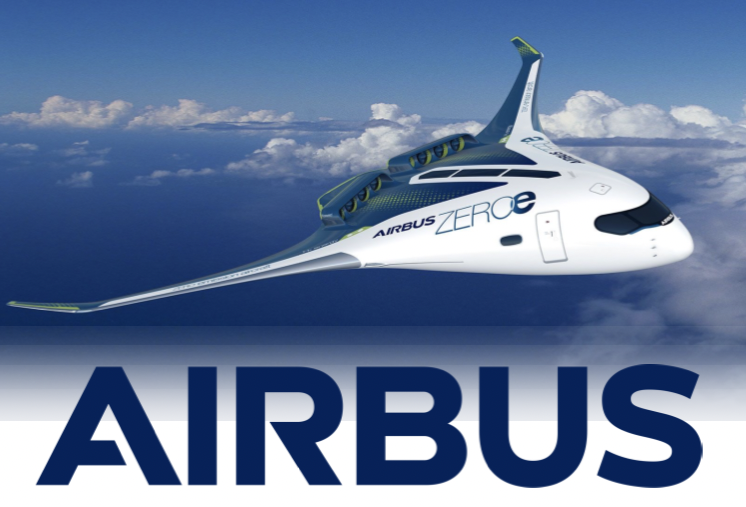
Legacy articles aren't reviewed and may be incorrectly formatted.
Talking Engineering 11: Andy Reynolds The Future of Zero-Emission Aviation
Conducted by Max Hersov, November 2022
It is estimated that the Aviation sector accounts for 3.5% of global warming, releasing into the atmosphere more than 900 million tonnes of CO2 per year.Airbus, the world’s largest aircraft manufacturer, is at the forefront of research into sustainable aviation, and is pioneering the development of commercial Hydrogen aircraft with their ZEROe concept planes.
Max Hersov spoke with the Head of Airbus ZEROe Hydrogen Storage and Distribution Systems, Andy Reynolds, who described Airbus’ plan to fly the world’s first zero-emission commercial aircraft by 2035.
MH: How close do you think we are to having commercial Hydrogen aircraft flying?
AR: We are already in the realm of hydrogen planes; not Airbus, but other companies have already made small, two-seater hydrogen aircraft. In terms of commercial planes, Universal Hydrogen will probably fly something around 20 seats in the next few months. It entails a retrofit in one of the engines and so is really still a flight test. In terms of real commercial operations where aircraft are actually flying and taking paying passengers, I’d say we are still a decade away. We at Airbus have targeted 2035 to enter service; and although that seems a long time away, new developments take time in aviation. It isn’t just about getting something flying and doing a test; we’ve got to actually understand all of the science, and what will happen if things don’t go quite the way we want to. We need to have many things in place to cope with that. We won’t feel comfortable until we’re sure that you are just as confident boarding a hydrogen plane as you are a kerosene plane today. And right now that feels around decade away.
MH: In pushing for sustainability in aviation, what puts Hydrogen above, say, electric aircraft?
AR: For electric aircraft, the power density just isn’t there. With today’s batteries, such as the ones in electric cars, you’d have to have more than the weight of the aircraft in batteries in order to do what an aircraft does today. The only feasible application for electric aircraft is on the scale of a couple of passengers, on commuter distances i.e. urban mobility. A lot of money is being put into that, but on the scale of an Airbus, it just doesn’t work with today’s technology, or even with technologies that we can see coming.
Sustainable aviation fuel looks to be a big part of greener aviation in the near future: the predictions made for aviation to be at net zero by 2050 are based almost half on sustainable aviation fuel.
Other fuels that have been looked at such as methane and ammonia all have various disadvantages compared to Hydrogen. The beauty of Hydrogen is that it is tremendously light, it has an incredible energy density by mass, and it is a product that is going to be at the heart of powering society in some decades time. Even if not, it will be a key ingredient in sustainable aviation fuel, so it will be available at a reasonable price all around the world, and we want to create an aircraft which can take advantage of that.
MH: In developing a Hydrogen aircraft, or one with a different fuel, do you need different engines, or how does the fuel you use change what the plane looks like and how it flies?
AR: We’re still looking into two distinct ideas with the engine. The first is an engine which is similar to today’s engines, so a turbojet (or probably a turboprop in the end), in which the combustion of hydrogen and general engine design is broadly similar to that of a kerosene engine, (even though the specific design around how you combust hydrogen is slightly different). The second is a fuel cell, which you power with Hydrogen to generate electricity, which drives a motor which drives a propellor.
So between those two families of propulsion, deciding which one is going to work is a really important decision. Much of what we are doing now is working towards being able to make that decision. We’re not ready to make that decision yet. We are just now getting demonstrators launched and once the analysis and assessments have been completed over the next few years we hope to make the decision to proceed to the first commercial aircraft.
Both of these options will be using liquid hydrogen storage, meaning that hydrogen will be stored at around 20 Kelvin in the rear of the fuselage in double-walled tanks with a vacuum in between the two walls to maintain those cryogenic temperatures at a few atmospheres of pressure. This is a bit of a challenge obviously. Storing fluid at 20K in a plane which is accelerating, changing altitude, pitching and banking and going through turbulence is not easy.
MH: Both on the ground and in the air, and during the refuelling, how do you manage to deal with such low temperatures, keeping the hydrogen at 20K while still being energy efficient?
AR: Making green hydrogen requires energy from green sources. At the moment it is created from the electrolysis of water, which itself takes a lot of energy. Then, you need another chunk of green electricity to liquify the hydrogen using classical liquefaction techniques: essentially repeatedly depressurising it. Today, this takes place in a few large refineries in Europe [and elsewhere] and liquid hydrogen is trucked across the continent, which isn’t great. However, we plan on liquifying at the airports themselves.
Once you’ve got it in a liquid form, you just have to make sure that the whole chain from point of liquification to the storage tank on the ground and then in the aircraft from the fuel tank to the engine is incredibly well insulated, and managing the pressure and the temperature - getting the thermodynamics right - is a large part of what we’re designing the system to do. So, in the aircraft it is not just of simply pumping some of that from the tank to the engine. You are actively managing that system throughout the flight. As you take fuel out of a closed tank, you have to return some of the flow back into the tank as a gas to maintain the pressure.
Those techniques are well known; they are used to store hydrogen industrially right now, but the difference is is that this does not happen on a moving, dynamic platform which is an aeroplane. Rockets such as the Ariadne have liquid hydrogen tanks, and they take off in quite a spectacular style, but their take-off run is only a few minutes. They are constantly refuelling right until a few seconds before takeoff: the piping and scaffolding that separates off from the rocket at the last second is actually them stopping refuelling. Hydrogen is escaping and being burnt at the same time. That is of course not a solution for us: we’ll need to maintain it for hours, and thus will need various forms of insulation as well as active systems maintaining the temperature and pressure within the tank. Research into how you do that reliably, and with a very high level of safety, is what our teams are now working on.
MH: What will the fuel tanks be made of?
AR: We are targeting to use aluminium for both walls, which means that we will have to learn how to weld aluminium and learn about the characteristics of its alloys at super low temperatures. For the future, there are lots of people looking at composite tanks. In trucks and buses using hydrogen, the state of the art is composites. However, they are storing gaseous hydrogen at room temperature, and if you try to use that technology for a vacuum, you actually find that some of the resin within the composite actually leeches out of the composite, meaning that it is quite difficult to maintain a vacuum because the composite actually breaks down into it. Nevertheless, right now there is a huge amount of research going into composite materials, which is great because it would give us a weight benefit - always exciting in aviation. Of course, we need the technology to work, and we need the tiny molecules of hydrogen to stay in the tank, since, being so tiny, they have a nasty habit of just wandering through what looks like solid walls. The big advantage of having them tremendously cold is that they don’t have much energy, and leak through the walls much less than at room temperature.
MH: How will you ensure that the production of hydrogen is eco-friendly?
AR: This relies on the wider energy ecosystem and other companies / other infrastructure being in place. Airbus doesn’t have resources to generate enough green hydrogen for itself. We are speaking about eye-watering amounts of energy, and this requires society as a whole to move away from hydrocarbons to green energy. In the future, we believe that hydrogen will likely be a large store of green energy and there will be global-scale hydrogen ecosystem beyond aviation, with hydrogen being shipped around much as oil and gas is shipped today.
AR: Recently, our CEO said that the pace of change for sustainable aviation is governed by the availability of sustainable aviation fuel, as right now we could be flying our planes on 50% or more sustainable fuel. We need companies, especially those already in petrochemicals, making investments in the right places for sufficient scale. There is a tremendous future opportunity for companies who make the right decisions now.
MH: Will Airbus be the first to fly commercial hydrogen airplanes?
AR: That is our stated ambition, to be there by 2035. We do have an extremely capable competitor called Boeing, although they have had a few setbacks in recent years. And there are also other competitors around the world, as well as a lot of venture capital trying to find the ones who will make the breakthrough, although as I said, lots of people are focusing on smaller, urban mobility aircraft.
MH: Airbus often references three particular concept airplanes. What are the particular strengths of each of them, especially the blended wing aircraft, which looks completely different to conventional planes?
AR: The blended wing aircraft is the one that ‘gets the most clicks’ per se, as it looks so novel and cool, I suppose. Aerodynamically it has a lot of advantages over the ‘tube and wing’ design, which is prevalent right now. So, aerodynamically that would be the way to go if we could get there. But, it would be a huge step, even apart from the hydrogen, to get there. Industrially, it is a different type of manufacturing and from a certification perspective there are a range of new challenges to overcome, such as how you get onboard, and how you get out of the aircraft, in crash-worthiness analysis etc. But of course there is a big carrot dangling there in the way of aerodynamic efficiency, if we could make the other things work.
The turboprop that we have is the most straightforward of the three, with advantages in the efficiency of propellor design, but disadvantages in terms of speed, even though this does increase efficiency. It is the easiest to certify of the three, and probably the lowest risk, although it has disadvantages in terms of size and speed.
The third one, which looks more like a classical aircraft, is our ambition. What we say on our website is that our first aircraft in 2035 is going to be around ‘100 seats and 1000 nautical miles’. And although distance-wise this probably covers more than 50% of flights today, we want to get to an aircraft which is A320-sized, which all the major airlines, particularly EasyJet, use. We need to get a product which is hydrogen-powered in that space (more like ‘200 seats and 2000 nautical miles’). If we can get to there, then we have the bread-and-butter covered. We deliver up to 60 of those a month, more than 700 a year, which is obviously a huge percentage of our turnover. So we want a product in that market, although it probably won’t be the first one we do.
The decision I mentioned earlier about fuel cells or turbo-machinery is fundamental as well, because if you are using a propellor, you have the option of a fuel cell which is exciting in term of emissions. If you have something that looks like an A320, then you are looking at a turbo machine, and are burning hydrogen. Due to the high temperatures, this still leaves things to solve, such as NOx, particulates and contrails, which are important to address in creating a completely zero-impact airplane, not just a Carbon-zero one.
MH: Is that the main advantage of fuel cells over combustion engines?
AR: One of the main reasons for doing the demos is looking at what the aircraft leave behind in the atmosphere. With fuel cells, although you are producing a lot of water, we believe it is not in a form which will create a lot of contrails. It is just water. There are no high temperatures with nitrogen, and thus it will not generate NOx. So we believe with a fuel cell you can get to just generating water, which is a beautiful place to be. However, the energy that you need to power a large aircraft is considerable - on the megawatt scale. Now we’re already getting towards running fuel cells at megawatt scale in the labs, but we need to take that into the real world and see how that works in flight. We also need the reliability and operability required in commercial aviation. EasyJet and BA, and all of the airlines today will often use planes 14 hours a day, every day, and they will rely on their planes being operable all the time.
MH: Aren’t contrails just water vapour and why are they bad?
AR: Contrails are indeed just water vapour: they are ice crystals formed from water vapour. The science around contrails is really complicated and not very well understood today, but the science seem to point that persistent contrails, the ones that hang around for a long period of time, which you get on a relatively small percentage of flights, have a significant impact on the reflection of heat in the atmosphere. Some persistent contrails are good, because if they are in the right place and it’s daytime then they actually reflect sunlight away from the Earth, while others at a different time of day, will trap heat. It’s a small minority of flights for a small minority of the year but the science seems to be saying (with a huge margin of error, easily as big as the impact that we think it might have), that they are problematic for driving climate change. So, we’re funding a lot of research into that. Interestingly, we think that with the right air traffic control and the right flight management [routing], we might already be able to do something significant even with today’s engines, as contrail formation is dependent on local atmospheric conditions.
Many thanks to Andy Reynolds for his valuable time and insight.