Superalloys in Aerospace
An introduction to the incredible materials which make modern aviation possible.
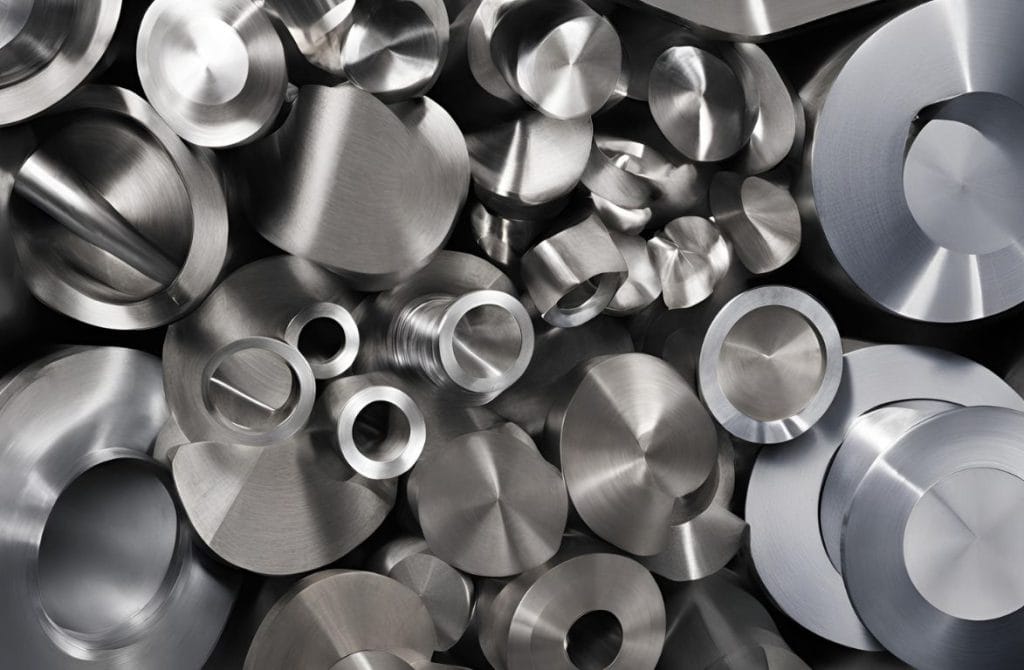
Sitting directly behind the Jet Engine’s burner section, the high-pressure turbine receives the full brunt of the hot exhaust gases leaving the combustion chambers, exposing its blades to temperatures upwards of 1200 degrees Celcius and putting them under immense mechanical stresses. It is hardly surprising that the ability of the metal alloys making up the turbine blades to maintain their structural integrity in such a harsh environment has earned them the exotic name “superalloys”.
Although metals typically have relatively high melting points, most undergo a drastic drop in tensile strength well below it, as an increase in the thermal energy of the atoms makes it easier for dislocations or indeed individual atoms to move through the metallic structure, thus costing the metal much of its strength and making it extremely vulnerable to creep: the gradual plastic deformation of a material under a continuous stress, even one which is considerably lower than its UTS. (Mathew & Steven Donachie, 2002, p.2)
Mechanical creep can be a fatal issue for turbine blades, as even slight distortions in their shape can have significant adverse effects on the efficiency of airflow handling and even possibly lead to catastrophic failure. It is primarily the unique microstructure of the superalloys that helps them suppress creep and maintain their strength at high temperatures, thus allowing the jet engine to run safely and effectively at the most demanding levels of power output.
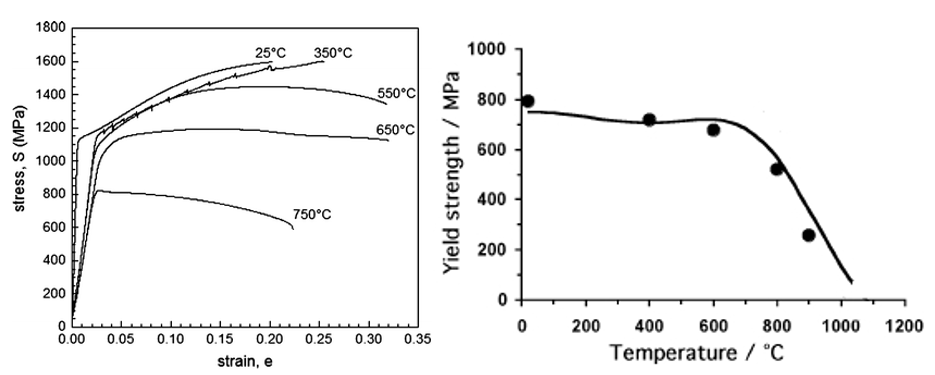
Of the three elements which can form the solvent of a superalloy, Nickel is generally preferred over Cobalt and Iron in the aerospace industry because of the consistency with which it maintains its FCC (Face-centred cubic) structure, making it easier for other alloying metals to be reliably added to the matrix; using Cobalt, on the other hand, is made more complicated by the fact that it transitions from HCP to FCC as its temperature increases. (Mathew & Steven Donachie, 2002, p.2)
The 𝛾 phase is the default state that Nickel-based alloys take when a small amount of another metal is added; the distribution of the elements in the lattice is largely random and it is relatively easy for individual atoms and dislocations to move through the structure. However, once enough Aluminium or Titanium is added, it becomes thermodynamically favourable for the alloying metal to form its own regular lattice within the structure, positioning its atoms at the corners of the unit cell.
The energy barrier for a nickel atom to move into a vacancy within the Aluminium/Titanium lattice is much higher than in the 𝛾 phase, thus making it harder for dislocations to propagate through the structure. This gives the intermetallic 𝛾′phase hard and brittle properties similar to those of an amorphous substance such as glass or ceramic. What makes superalloys truly stand out is just how much of the intermetallic phase they contain, usually making up to 70% of the blade; were they to be entirely made out of this phase, the turbine blades would be incredibly strong but also far too fracture-prone, risking catastrophic failure once the elastic limit is exceeded. (Ijaz, 2023)
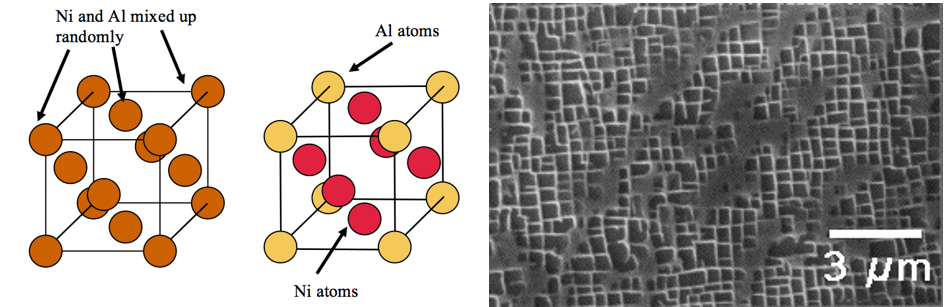
The carefully-balanced metallurgical compromise that solves this dilemma consists of combining the two phases by precipitating nanoscopic “bricks” of 𝛾′ within a “cement” of 𝛾. Although making up a minority of the alloy, the continuous 𝛾 phase allows the blade to maintain a degree of flexibility while the 𝛾′ phase provides the necessary tensile strength and creep resistance under high temperatures.
Having the same FCC structure allows the two phases to fit together coherently within the superalloy. (Bhadeshia, 2003) In fact, the phase boundaries prove to be a great barrier to the propagation of dislocations, typically requiring the synchronised movement of two dislocations (often called a “super dislocation”) to effectively overcome the aforementioned energy barrier of the Aluminium/Titanium lattice and pass from the 𝛾 to the 𝛾′ phase.
Another way of strengthening the superalloy is limiting the amount number of grain boundaries: although blocking movement of dislocations at low temperatures, the typical polycrystalline structure become a serious liability at high temperatures because the grain boundaries can act as high-speed pathways for diffusion - the movement of individual atoms through the metal which contributes to creep. (Bhadeshia, 2003) Furthermore, at extreme stresses the metal’s crystals could even begin to slide past each other each other along the boundaries, exacerbating plastic deformation and even potentially leading to fracture formation.
This can be solved through directional solidification while casting the superalloy – a process in which one end of the mould is kept significantly colder than the other, achieving uniform solidification of the metal from the bottom up and forcing the direction of the crystals forming throughout the blade to align. The most advanced superalloys take this concept to the extreme by passing the cooling alloy through a grain selector, which’s intricate structure is designed to allow the blade to form as one continuous crystal, thus completely eradicating the presence of any grain boundaries. (McClements, 2023)
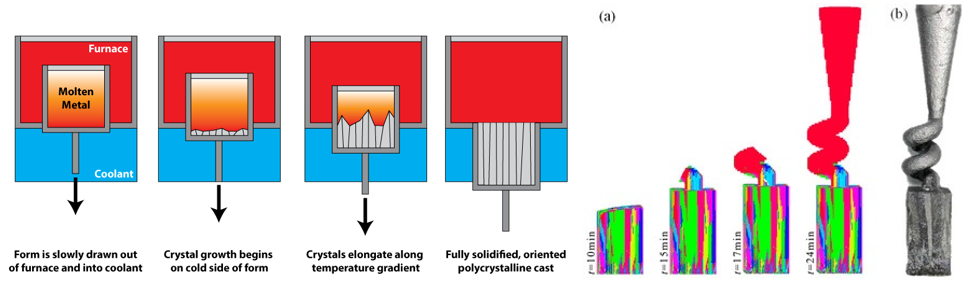
Many other metals are added to further strengthen and optimise the superalloy; Chromium is the most ubiquitous and arguably the most indispensable (Aeether, 2021), as it is the main element responsible for protecting the blades from corrosion through oxidation in the turbine’s harsh environment, which it achieves by forming a protective film of Cr2O3 on the alloy’s surface. Smaller amounts of solid solution strengthening elements like Molybdenum, Iron, Cobalt and Rhenium are often added to the 𝛾 phase and metals like Tungsten, Niobium, Tantalum and Vanadium to the 𝛾′phase. Modern turbine blades can also be coated in an additional ceramic layer of Zirconia (ZrO2) for even better resistance to corrosion. (Okura, 2015, p.7)
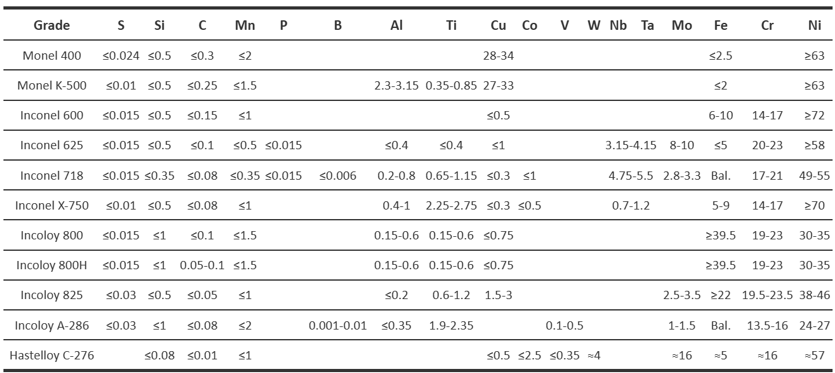
Ultimately, the decision of which additional elements to include is one which is incredibly complex and highly dependant on the specific application for which a superalloy is being developed. For example, members of the Inconel family are most commonly used in aerospace applications and thus need to prioritise the ability of the superalloy to maintain tensile strength and resist creep under high temperatures and stresses. Hastelloy superalloys are made for superior performance in the corrosive environments of the chemical and petrochemical processing industries; therefore, they contain a much larger amount of Molybdenum (up to 25% according to Aeether) to provide additional protection against oxidising and reducing agents.
This example is a great insight into the vast variety of fields in which different superalloy designs have found useful applications: from aerospace to nuclear energy, superalloys allow each industry to stretch to the limits of its potential without being held back by the material constraints of its components.
Bibliography
Aeether, (2021), The Role Nickel Plays in Superalloys, https://www.aeether.com/AEETHER/media/chemical-element/index.html [Accessed 25/01/2025]
Bhadeshia, H. K. D. H., 2003, Nickel Based Superalloys, https://www.phase-trans.msm.cam.ac.uk/2003/Superalloys/superalloys.html [Accessed 25/01/2025]
Bhadeshia H. K. D. H., 2003, Rafting in Nickel Based Superalloys, https://www.phase-trans.msm.cam.ac.uk/2003/Superalloys/rafting.html [Accessed 25/01/2025]
Donachie, M. J., Donachie, S. J., 2002, Superalloys: A Technical Guide (2nd Edition). United States of America: ASM International.
Forrest, K., (n.d.)., 5 Types of Superalloys, https://blog.brennaninc.com/5-types-of-superalloys [Accessed 25/01/2025]
Ijaz, F., 2023, Nickel Superalloys – the need of the modern aerospace industry, https://medium.com/@faisal_ijaz1991/nickel-super-alloys-the-need-of-the-modern-aerospace-industry-7ffd7fbb1552 [Accessed 25/01/2025]
McClements, D., 2024, All About Superalloys in Manufacturing, https://www.xometry.com/resources/materials/superalloys/ [Accessed 25/01/2025]
Metal Supermarkets, 2023, What is a Superalloy: Types, Manufacturing & Applications, https://www.metalsupermarkets.co.uk/superalloys-types-manufacturing-applications/ [Accessed 25/01/2025]
Okura, T., 2015, Materials for Aircraft Engines, https://www.colorado.edu/faculty/kantha/sites/default/files/attached-files/73549-116619_-_takehiro_okura_-_dec_17_2015_1027_am_-_asen_5063_2015_final_report_okura.pdf [Accessed 26/01/2025]